

设备改善“特种兵”,技能赛场“常胜队”
发布时间:2023-06-09 10:59:51
设备改善“特种兵”,技能赛场“常胜队”
通讯员 袁尹 张航伟
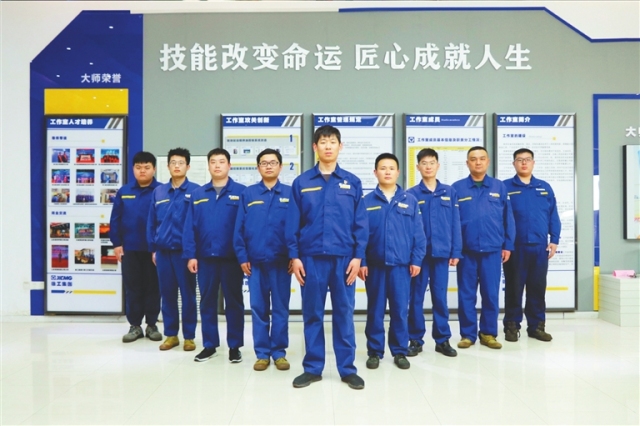
徐工重型设备能源部班组
在徐工重型设备能源部,有这样一支设备改善班组,他们的平均年龄只有25岁,却个个身怀绝技,既是设备改善的“特种兵”,也是技能赛场的“常胜队”,班组先后培养出6名全国技术能手、2名江苏省技能状元,是一个名副其实的技术尖刀班。
“139”模式打造金牌工匠
为快速培育高技能人才,班组借助公司金牌工匠项目,形成一套特色“139”维修人才培养模式,即“每天1小时培训、每周3专题讨论、9项技能提升机制”。这种模式正是班组员工从技术小白到技能大咖的成长法宝。
经过层层选拔,一部分技能精英走上了竞赛的舞台。备赛期间,他们秉持工匠精神,发扬战斗精神,坚持24小时作战,一天当作三天干。为了达到肌肉记忆的效果,他们每天重复着相同的动作数百遍,练、一直练、练到手比脑子快。每天长达15个小时枯燥乏味的训练,他们和自己“谈判”、和自己“竞赛”,苦、咬咬牙,累、再坚持坚持,“不负自己、不负企业、不负国家”成了训练员工的座右铭。实操训练结束后,他们上网查阅资料,总结、提炼新技术、新知识。
在比赛场上,他们冷静发挥、顽强战斗,数次摘得维修技能大赛桂冠。近年来,黄实现、袁雪雷、韩东泽、邵伟、赵红楼、刘子豪、吴若尘、李鹏龙等10余名班组青年员工,荣获国赛一等奖10人次、二等奖2人次、三等奖3人次,省赛一等奖22人次、二等奖7人次、三等奖5人次,其中6人荣获全国技术能手称号、2人当选省技能状元。
正是这种积极奋进的学习和竞争氛围,造就了一个又一个全国技术能手,设备改善组也成为徐工重型有口皆碑的全国技术能手班组。
深耕设备本质可靠性提升
近年来,随着公司产能结构的变更,传统的设备维修保障模式已无法满足发展需要,公司提出“设备用不毁”的理念。为了提升产能,提升设备运行可靠性,班组肩负起了公司设备预防管控标准体系建设,将竞赛所学机床装调与维护工艺标准带到实际工作中,编制设备点检、设备使用规范、设备预防性维护、易损件更换等210多类设备预防管控作业标准,规范了企业内部设备操作、点检、维保作业标准。
为了破解大型加工中心点检修困难的难题,班组将竞赛中使用的激光干涉仪、球杆仪、微型探测器等先进仪器带到实际工作中,创立“设备免拆卸点检透析法”“设备误差精度快速检测调整法”等五大操作方法。
随着MES、SCAD等数字化平台的建设与应用,团队成员探索微型传感技术的应用,联合国内顶尖机床生产厂家,首创国内设备健康监控平台,实现设备各机构运行状态的实时监控、异常预警、维保提示等。经过不断分析改进设备预防管控方法,实施精准预防,近5年设备单位工时故障率降低67%。
推动绿色工厂建设
在公司智能制造项目中,班组成员深入探索公司在设备能源工艺保障中的不足,承接公司智能能源系统建设项目,利用信息化技术、自动化技术,搭载5G网络,集成全厂与32个能源站房、18套能源系统运行数据,开发精细化用能供应模型,建成一站式能源集控平台。通过采集全厂区水、电、气等7种介质,1484块能源仪表数据,开发能源精细化管控模型为生产提供指导,建成了多厂区一体化智慧型、精细型、可靠性型能源管理系统,节省运行人员12人,每年节省能源费用482万元,助力公司多次荣获江苏省“能源管理体系认证优秀组织”及“节水型企业”等称号。
攻坚设备自动化加工难题
班组成员以项目历练为抓手,针对长久以来起重机三大主体结构件加工效率低、过程保证能力不足的问题,进行专项攻坚,解决结构单元自动化加工难题。通过推动工装自动定位、设备自动检测、程序集成加工以及加工过程稳定性提升,实现车架、转台、伸臂加工19台大型加工中心自动化加工应用,设备利用率提升16%,产品加工过程保证能力大幅度提升;利用数字孪生技术,在转台线后尾加工单元实现设备运行数据、产品加工过程、线体物流信息的实时监控、可视化展示和远程控制,在行业内率先实现大型结构件生产加工单元少人化生产,推动大型结构件生产从单机自动化向“一人多机”加工模式迈进。
他们还利用SCADA平台,统一设备“两率”数据采集分析标准,深度分析“两率”异常问题,推动设备、工装问题解决,拉动计划、物流协同改善,近3年来主要设备平均利用率由41%提升至53%。
青春正当时,风好正扬帆。作为企业设备改善“特种兵”,班组将进一步以新能源技术创新“先手棋”,积极参与智能4.0工厂建设,“节”尽所能应对“双碳”大考,为企业高质量发展涂上绿色化、数字化、智能化的浓厚底色。